Overview of steel rebar finishing rolling Tungsten Carbide Mill Rolls For Steel 100% Pure Powder of WC & CO Carbide Rolls
Metal powder is a common form of metal that has been processed into fine particles, ranging from a few micrometers to over 100 microns in diameter. It plays a crucial role in various industrial applications due to its unique properties and versatility.
Features of steel rebar finishing rolling Tungsten Carbide Mill Rolls For Steel 100% Pure Powder of WC & CO Carbide Rolls
Physical Characteristics
Particle Size: Ranging from nanometers to hundreds of micrometers, the size distribution significantly influences the powder’s flowability, packing density, and sintering behavior.
Shape: Particles can be spherical, irregular, flake-like, or dendritic, each shape affecting the final product’s mechanical properties and surface finish.
Purity: Depending on the production method, metal powders can achieve high levels of purity, critical for applications like electronics and aerospace where impurities can degrade performance.
Density: While less dense than their solid counterparts due to the presence of air between particles, metal powders can be densely packed during processing to approach the density of the solid metal.
Chemical Properties
Reactivity: Some metal powders, particularly aluminum and titanium, are highly reactive with air and moisture, necessitating careful handling and storage under inert atmospheres or vacuum.
Oxidation: Exposure to air can lead to surface oxidation, forming a passive layer that affects sintering and other processes. This can be managed through surface treatment or use of protective atmospheres.
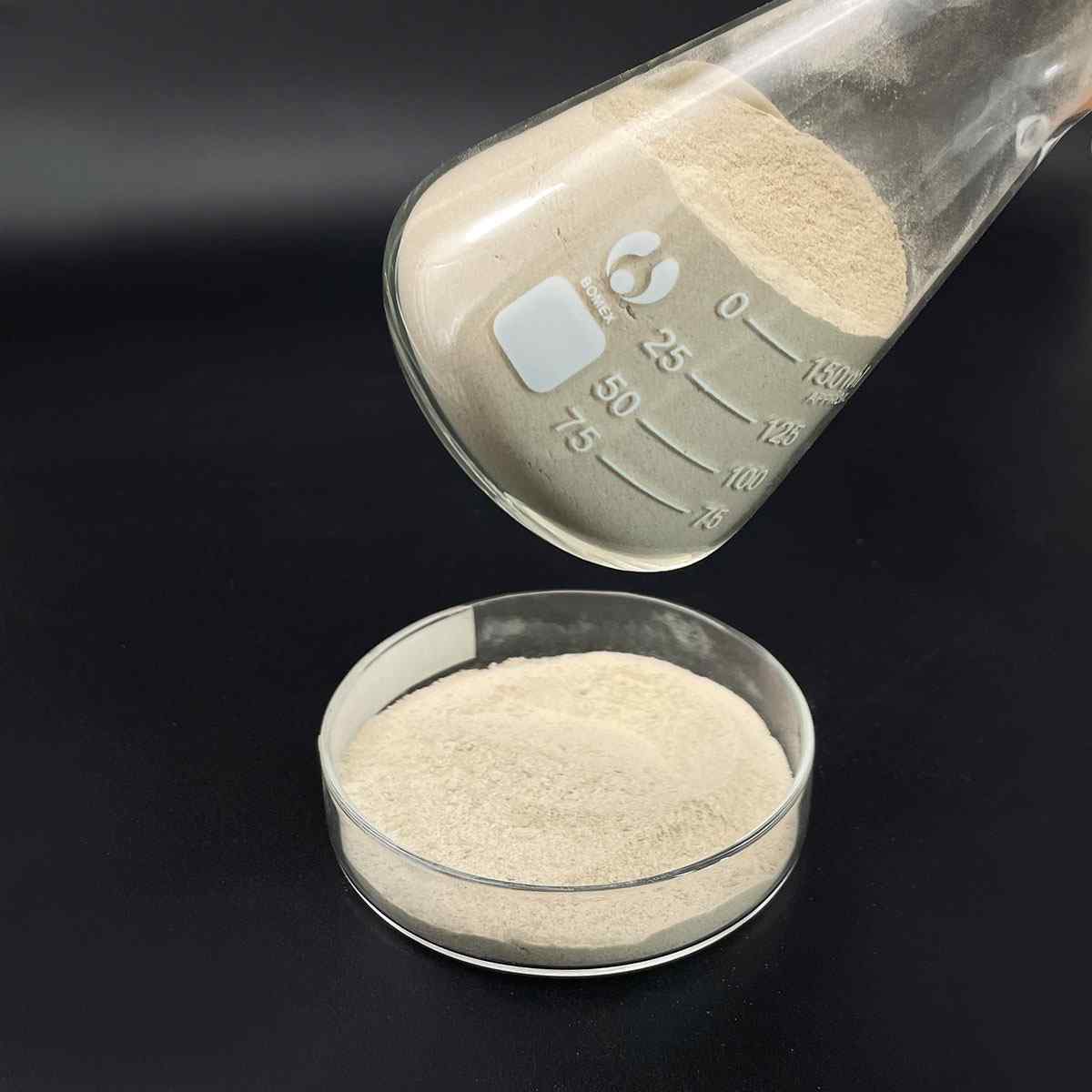
(steel rebar finishing rolling Tungsten Carbide Mill Rolls For Steel 100% Pure Powder of WC & CO Carbide Rolls)
Parameters of steel rebar finishing rolling Tungsten Carbide Mill Rolls For Steel 100% Pure Powder of WC & CO Carbide Rolls
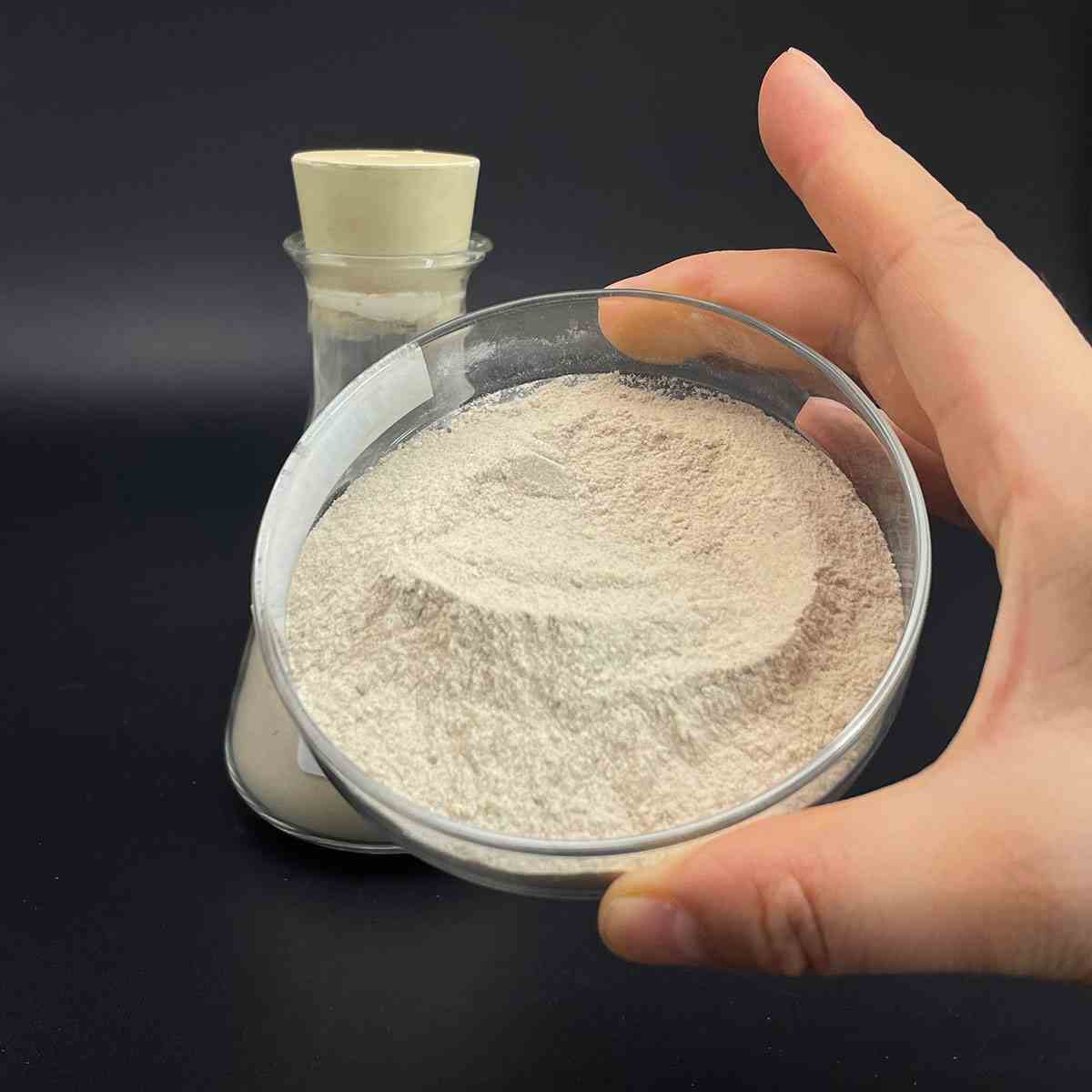
(steel rebar finishing rolling Tungsten Carbide Mill Rolls For Steel 100% Pure Powder of WC & CO Carbide Rolls)
FAQs of steel rebar finishing rolling Tungsten Carbide Mill Rolls For Steel 100% Pure Powder of WC & CO Carbide Rolls
Q1. What is steel rebar finishing rolling Tungsten Carbide Mill Rolls For Steel 100% Pure Powder of WC & CO Carbide Rolls, and how is it made?
Metal powder consists of fine metallic particles that have been processed from larger metal pieces. Common production methods include atomization, where molten metal is sprayed into tiny droplets that solidify into powder; chemical reduction, which converts metal compounds into elemental metal powders; and mechanical processes such as grinding.
Q2. Why are metal powders used instead of solid metals in manufacturing?
steel rebar finishing rolling Tungsten Carbide Mill Rolls For Steel 100% Pure Powder of WC & CO Carbide Rolls offer several advantages, including the ability to create complex shapes through processes like powder metallurgy and additive manufacturing without needing further machining. They also allow for the production of porous or composite materials, and can result in less material waste.
Q3. Are all metal powders the same, or do they vary in composition and properties?
Metal powders can vary greatly depending on the base metal or alloy, particle size, shape, and purity. Different compositions suit specific applications, from iron and steel powders for structural components to titanium and aluminum powders for lightweight, high-strength parts.
Q4. How does particle size affect the performance of steel rebar finishing rolling Tungsten Carbide Mill Rolls For Steel 100% Pure Powder of WC & CO Carbide Rolls?
Particle size influences the flowability, packing density, and sintering properties of steel rebar finishing rolling Tungsten Carbide Mill Rolls For Steel 100% Pure Powder of WC & CO Carbide Rolls. Finer powders generally have a higher surface area, which can enhance reactions or bonding during sintering but may also increase the risk of agglomeration or require special handling due to dustiness.
Q5. What safety precautions should be taken when handling metal powders?
Given the potential for fire, explosion, and respiratory hazards, appropriate safety measures include using personal protective equipment (PPE) such as respirators and gloves, storing powders in a dry, cool, and controlled environment, avoiding sparks and open flames, and ensuring adequate ventilation to minimize dust accumulation.
Q6. Can steel rebar finishing rolling Tungsten Carbide Mill Rolls For Steel 100% Pure Powder of WC & CO Carbide Rolls be recycled or reused?
Yes, many steel rebar finishing rolling Tungsten Carbide Mill Rolls For Steel 100% Pure Powder of WC & CO Carbide Rolls can be reclaimed and recycled, either directly back into the production process or after suitable treatment. Recycling helps reduce waste and raw material costs.
Q7. How does steel rebar finishing rolling Tungsten Carbide Mill Rolls For Steel 100% Pure Powder of WC & CO Carbide Rolls contribute to sustainable manufacturing practices?
By enabling efficient use of materials through near-net shape production, minimizing waste, and allowing for the recycling of scrap and unused powder, metal powder technologies support sustainability goals. Additionally, advancements in additive manufacturing using metal powders can lead to lighter, more energy-efficient products.
Q8. What are some common applications of metal powders in daily life?
Metal powders are used in a wide range of everyday items, from car engine parts and bicycle components made through powder metallurgy to the coatings on kitchen appliances for durability and corrosion resistance. They’re also found in electronic devices, batteries, and even some medical implants.
Inquiry us